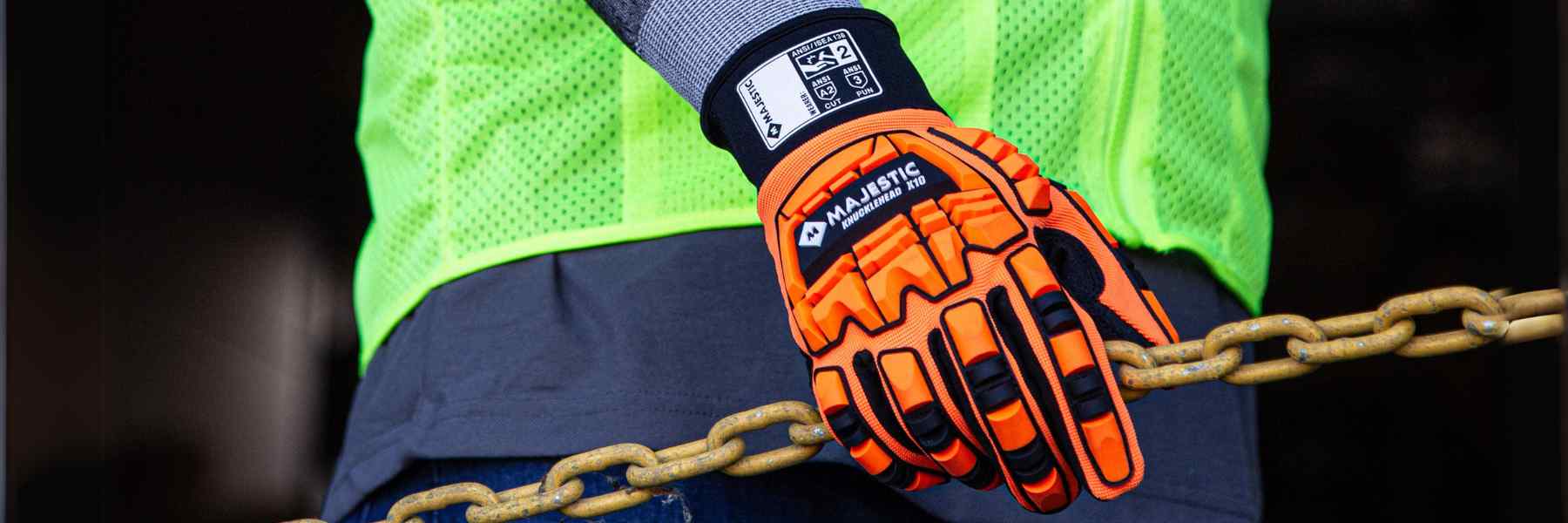
ANSI and EN Safety Standards
Safety standards are essential to manufacturing and using equipment across various industries. The American National Standards Institute (ANSI) and the European Norms (EN) are two standards that ensure products meet specific performance and safety requirements.
By understanding the nuances between ANSI and EN ratings, manufacturers, employers, and consumers can make better safety equipment decisions. These standards ensure safety equipment can fit the needs of specific jobs and tasks.
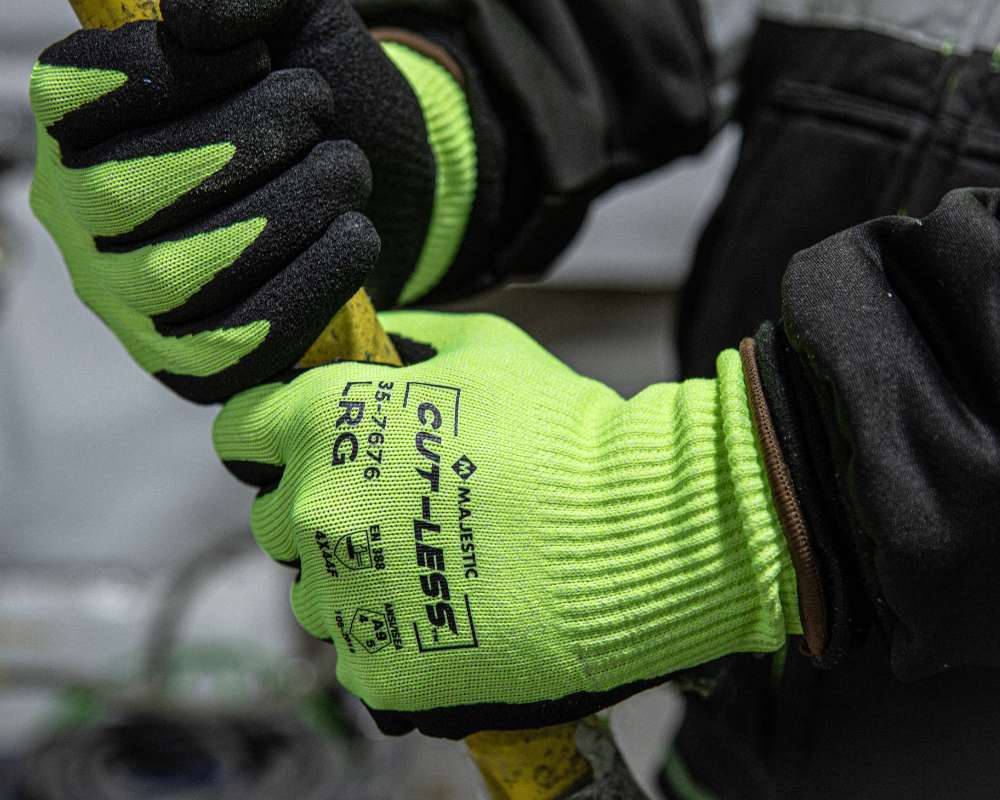
What Are ANSI Ratings?
ANSI is a private, non-profit organization that organizes standards for safety equipment. These ratings are created with input from industry experts, government agencies, and customer groups. Following ANSI standards isn't mandatory; however, OSHA references ANSI, and these standards are the generally accepted safety guidelines within the United States.
What are EN Ratings?
EN standards are adopted by European Union member countries. EN products undergo testing by an independent verifier to ensure they meet the required protection levels. Unlike ANSI, when these standards are adopted, they are legally enforceable. Service providers in EU member countries must follow these standards to market their products and services.
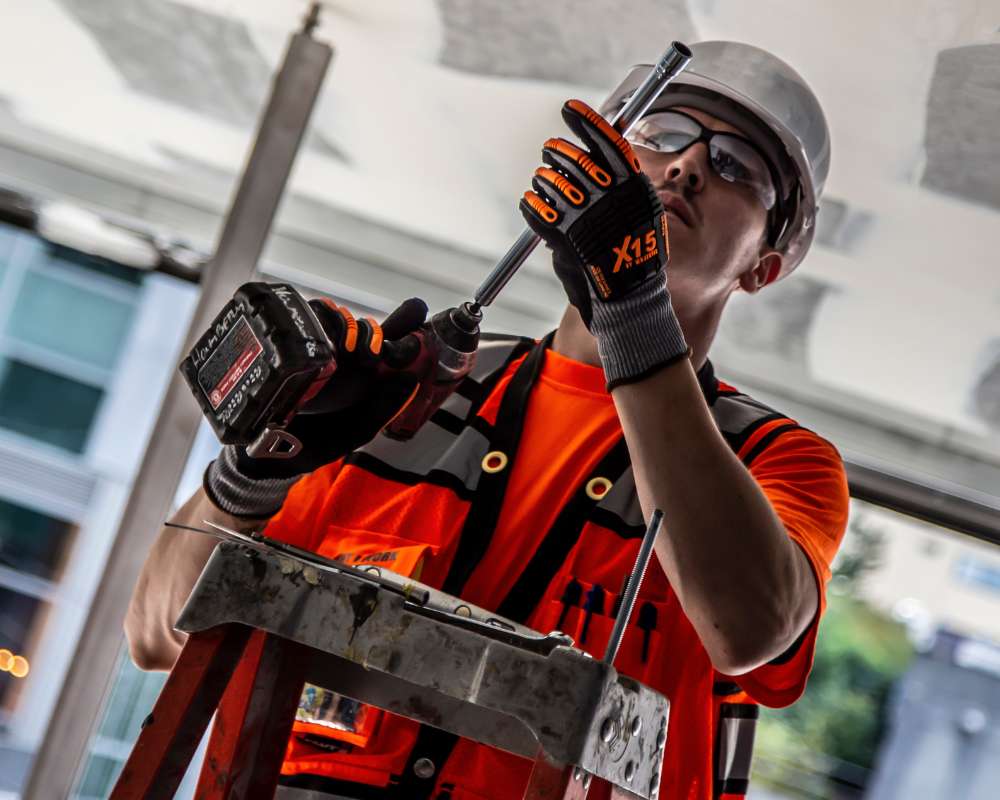
ANSI and EN Ratings Key Differences
Both ANSI and EN standards aim to ensure safety. However, their geographic applicability, creation process, and certification requirements differ. ANSI standards are widely recognized in North America and referenced globally, whereas EN standards become law in the EU and influence regulations in other regions.
How ANSI and EN Ratings Help
Safety ratings offer a dependable measure to ensure equipment meets or exceeds safety requirements, reducing the risk of workplace injuries. This standardization helps distributors make informed choices and builds trust among workers in the effectiveness of their equipment. ANSI and EN:388 standards promote high-quality materials and innovation, creating a safer and more efficient work environment.
Learn More About ANSI Standards
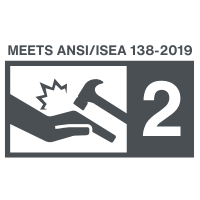
Impact Resistance
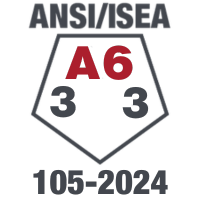
Cut Resistance
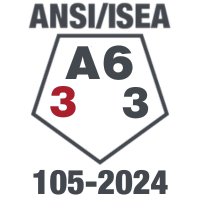
Abrasion
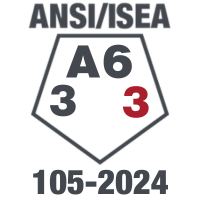
Puncture
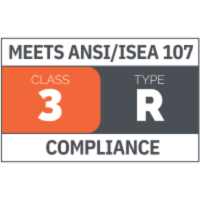
High Visibility
Updates & Revisions
ANSI and EN:388 safety standards typically change every few years to incorporate the latest safety research and advancements. Staying up to date with these changes is crucial for ensuring that workers receive the most effective protective equipment available. By keeping current with these standards, companies can better manage risks and demonstrate their commitment to employee well-being.